Collabomation: kollaborative Automatisierung in der Produktion
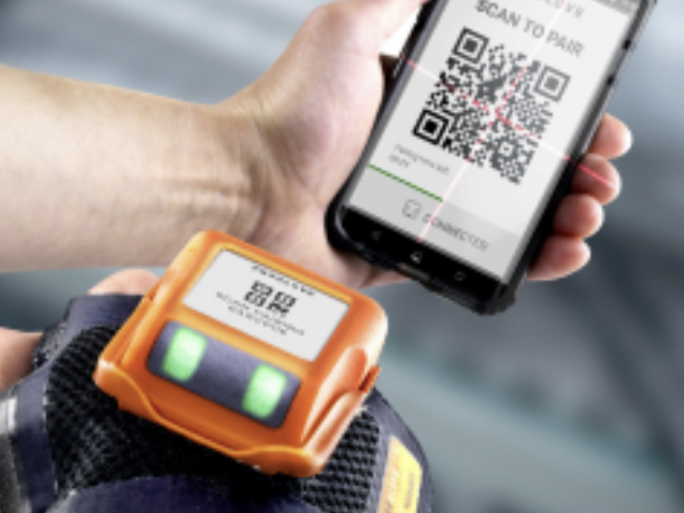
Wearables werden die meisten mit Gaming verbinden. Was haben sie in der Industrie zu suchen?
Stefan Lampa: Wie bei vielen anderen Anwendungen auch zeigt sich der Mehrwert gerade in der Industrie besonders deutlich. Anwenderunternehmen sind immer wieder überrascht, welche Potenziale sie mit Wearables erschließen können. Und das gerade, weil sie nie damit gerechnet hätten, dass sich mit einem scheinbar kleinen Eingriff in die Handhabung ein solch mächtiger Hebel bewegen lässt.
Das müssen Sie uns erklären.
Bei vielen manuellen Tätigkeiten kommt es auf die Hände an und die können mit Wearables eben meist frei bleiben. Das spart oft nur eine vermeintlich kleine Zeitspanne pro Handgriff. Wenn Sie aber immer wieder denselben Handgriff ausführen müssen, summiert sich das exponentiell. Ein Beispiel: Jeder Automobilbauer produziert pro Tag und Werk etwa 1.000 Autos. Dabei scannen die Werker etwa 1.000-mal pro Auto. Entfallen nun die Greifzeiten für einen konventionellen Scanner, sind das etwa 4 Sekunden weniger pro Scan. An einem einzigen Tag und pro Werk wären das also 4 Millionen Sekunden. Das sind deutlich über 46 Mitarbeitertage an einem einzigen Arbeitstag.
Wearable können also eine Lösung für Fachkräftemangel sein?
Wearables sorgen nur dafür Effizienz- und Ergonomiepotenziale zu heben. Das schafft Spielräume und zusätzliche Flexibilität. Mitarbeiter können dann für andere Aufgaben eingesetzt werden. Ihre Stellen fallen – jedenfalls nach unserer Erfahrung – nicht weg. Übrigens sind die Mitarbeiter meist ein entscheidender Treiber für den Einsatz von Wearables.
Weil sie ihnen lästige, repetitive Arbeit abnehmen?
Weil Wearables ihren Job einfacher machen, ihre Arbeitsqualität steigern, ihnen Wege sparen und sie bei ihrem Job im wahrsten Sinne entlasten. Wenn Sie an einem Arbeitstag pro Minute zweimal scannen müssen, was nicht besonders viel ist, kann die Entlastung sehr schnell mehrere hundert Kilo betragen. Denn Sie müssten dann am Tag 960-mal scannen. Ein konventioneller Scanner wiegt etwa 350 Gramm und ist damit mehr als 300 Gramm schwerer als ein Wearable. Das wären dann also mehr als 288 Kilo extra. Gewicht, das sie nicht mehr heben müssen. Und die Unterschiede können noch deutlicher ausfallen.
Sie verweisen immer wieder aufs Scannen. Barcodes sind doch ein Auslaufmodell, das RFID bald ersetzen wird?
RFID hat Vorteile, aber im Moment dominiert noch der Barcode. RFID wächst schnell, keine Frage. Aber auch der Barcode hat sich über die Jahre konsequent weiterentwickelt. Er ist gerade in der Industrie dank seiner Einfachheit und Robustheit vielfach die bessere Wahl! Deswegen zeichnet sich hier auch noch nicht einmal ansatzweise ein Ende ab. Letztlich ist das auch mehr eine Frage dessen, was man möchte. RFID gehört eher in den Dunstkreis der Prozessautomatisierung, wohingegen Barcodes letztlich immer etwas mit Menschen und manuellen Tätigkeiten zu tun haben.
Und damit stellt sich doch auch die Frage, ob KI, Robotik und Automatisierung den Menschen irgendwann komplett ersetzen können?
Da bin ich insbesondere nach meiner Zeit bei namhaften Robotik-Herstellern eher skeptisch. Die Technologie ist immens wichtig und gewinnt jeden Tag mehr an Bedeutung. Aber ich glaube nicht, dass in absehbarer Zeit ein Zustand erreicht wird, der den Menschen komplett überflüssig macht. Ehrlich gesagt wundere ich mich ein bisschen, woher diese Neigung herkommt, dass es immer das eine oder das andere sein muss. Schwarz oder weiß! Dabei zeigt sich doch in der Realität immer wieder, dass es eine Vielzahl von Grautönen gibt.
Ich sehe nur, dass viele Unternehmen verstanden haben, dass sie die Interaktion von Mensch und Maschine unterstützen müssen. Vollautomatisierung ist in vielen Bereichen aus unterschiedlichen Gründen schlicht nicht möglich. Teilautomatisierung dagegen schon. Autonome Mobile Roboter, fahrerlose Transportsysteme und Cobots können heute schon an vielen Stellen nahtlos mit Menschen zusammenarbeiten. Ich nenne das gerne kollaborative Automatisierung oder Collabomation.
Und was macht diese kollaborative Automation aus?
In erster Linie geht es darum, Schnittstellenproblematiken zu beseitigen. Das erfordert, dass sie die Werker vor Ort mit dem Internet der Dinge koppeln, damit sie maschinenlesbare Daten an diese Systeme übertragen können. Das können einfache Arbeitsanweisungen aber auch Transaktionsquittungen sein. Diese Daten dienen dazu, die Prozesse auf dem Shopfloor zu steuern und den Verkehr zu orchestrieren. Wir müssen überhaupt lernen, die Daten aus dem operativen Betrieb besser zu nutzen. Da lassen viele Unternehmen noch erhebliches Potenzial liegen.
Was genau meinen Sie damit?
Typische Enterprise-Anwendungen wie ERP oder WMS liefern eine Top-Down-Sicht. Das ist aber bestenfalls ein Idealbild. Das ist notwendig, aber ohne ein tatsächliches Bild, dessen, was vor Ort Sache ist, fehlt einfach etwas. Und diese Lücke muss man mit einer Bottom-Up-Perspektive schließen.
Ein Beispiel: In der Warenannahme scannen die Mitarbeiter die eingehenden Pakete. Die hinterlegten Informationen werden an das System übertragen. Aber nicht, wie oft ein Scan-Versuch gescheitert ist oder wie lange es gedauert hat, bis die Barcode Symbologie verarbeitet wurde. Sie können heute auch schon problemlos Hotspots erfassen und die Wegezeiten der Mitarbeiter ermitteln, um diese zu optimieren. Und diese Entwicklung ist noch lange nicht am Ende.
Klingt nach „Big Brother Is Watching You“.
Transparenz ist dabei unabdingbar. Und selbstverständlich dürfen Sie derlei Daten nicht personenbezogen, sondern nur anonymisiert verarbeiten. Entscheidend ist aber, dass dies wesentliche Entlastungen für die Mitarbeiter mit sich bringt, was diese durchaus goutieren. Sie müssen sehen, dass die Mitarbeiter im Lager 40 bis 60 Prozent ihrer Zeit damit verbringen, durch die Gegend zu laufen. Da ist immenser Raum für Optimierungen. Zudem können Sie über das Wearable auch Warnmeldungen an die Mitarbeiter ausgeben. Etwa: Trage einen Helm oder schnittfeste Handschuhe.
Sie sagten zu Beginn, dass sich der Mehrwert viele Anwendungen gerade in der Industrie besonders deutlich zeige.
KI leistet in der Industrie schon einen wirklich wichtigen Beitrag. Wir sehen das zum Beispiel deutlich im Bereich autonomes Fahren. In diesem Umfeld gibt es bereits eine Reihe von Anwendungen, die in der Industrie gut etabliert sind. Fahrerlose Transportsysteme beispielsweise. Im Konsumentenumfeld gibt es auch bereits Anwendungen wie Einparkhilfen. Das Umfeld erweist sich jedoch als weit diffuser. Wenn wir das perspektivisch betrachten, halte ich es für weit wahrscheinlicher, dass wir zum Beispiel auch beim Langstreckentransport automatisiertes Fahren auf begrenzten Abschnitten sehen werden. Das wird bereits viel früher da sein, als für die breite Masse der privaten Autofahrer.
ist CEO von ProGlove, das laut eigenen Angaben Wearable-Tech-Lösungen für Kunden aus den Bereichen Lager, Logistik, Produktion und Handel anbietet. Dazu zählen Unternehmen wie BMW, DHL, Gap Inc. oder Lufthansa Technik Logistik Services.